Optimizing Warehouse OperationsWarehouse Execution System
- Provider
- Toshiba Digital Solutions CorporationToshiba Corporation
The logistics industry has changed immensely in recent years. The pandemic kept people at home, and spurred use of e-commerce. Today, there are many more smaller parcels and packets to handle, more deliveries to be made, and the burdens on companies in the industry are increasing.
One of the most pressing problems, one found worldwide, is increasing difficulty in recruiting and retaining people with the right skill set. This is especially true for drivers; despite the industry’s efforts to provide a better working environment and conditions, it is more difficult than ever to find enough drivers.
With a smaller workforce and more packages to handle, there are growing concerns that the world will see a logistics crisis. This will only be averted if logistics companies overcome the challenges of realizing efficient warehouse operations and managing to deliver more packages with fewer people.
Many logistics companies are automating their operations with robots and material handling equipment to make work more efficient. But even if machines are introduced, it does not mean that efficiency will automatically improve. Even worse, efficiency may even decline if the roles of people and machines are not clearly defined and well-orchestrated.
When deploying machines and semi-automating a warehouse, in order to improve throughput, a mechanism that can forecast the future workload, and control/instruct the workforce and equipment is required.
Toshiba’s Warehouse Execution System (WES) maximizes utilization of all warehouse resources — people, robots, and material handling equipment.
While a Warehouse Management System (WMS) that supports people, and a Warehouse Control System (WCS) that controls individual machines have been available, they were not integrated, and efficient management of the people and machines in the warehouse relied on the knowledge and intuition of specific, experienced people. Relying on a specific individual has always been an issue in terms of business continuity, but now we no longer need to do that.
Our WES is a cloud service that interfaces with WMS and WCS. It collects and integrates data from people and machines in the warehouse and uses it for visualization, analysis and simulation, as well as optimization.
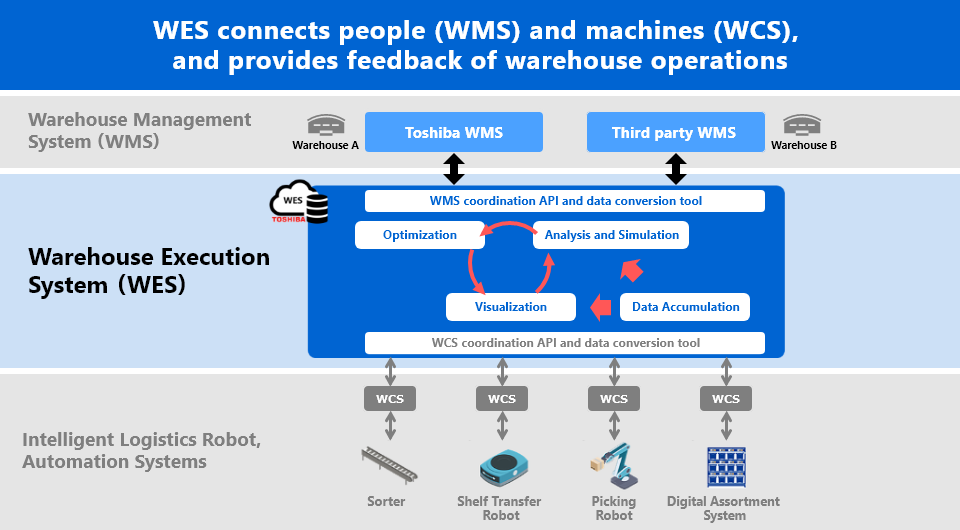
We have cultivated experience and know-how on logistics sites and warehouses through our own manufacturing business, and brought this know-how into our WMS.
Toshiba has been in manufacturing for close to 150 years; it’s in our DNA. We also have expertise in advanced robotics. Use our WCS to monitor and provide real-time instructions to sophisticated warehouse robots handling tasks like unloading, transporting, and picking items of various shapes, sizes, and weights.
Toshiba, the world number 3 in AI-related patents*, is rich in optimization technology resources. We bring these leading-edge capabilities to highly advanced optimization strategies built on data derived from WMS and WCS.
* World Intellectual Property Organization: “WIPO Technology Trends 2019 – Artificial Intelligence”
Knowledge from warehouses and robots incorporated into our WES, appropriately allocates work to people and robots. Taking into consideration the characteristics and abilities of people and machines, WES provides an optimal work plan that the WMS gives to people, and WCS sends to the robots. WES contributes to efficient operations within the entire warehouse, through real-time progress monitoring of people and machines, while also ensuring the flexibility needed to update the work plan in response to any sudden requirements
Toshiba's WES not only works with Toshiba's WMS, but it can also interface with third party WMS and WCS which customers may have already installed. We are currently verifying that our WES can interface with various systems and devices and give instructions to people based on a work plan optimized by an existing third-party WMS, as well as connecting and operating various robots and material-handling equipment with open API.
Like a veteran employee, Toshiba’s Warehouse Execution System (WES), can handle advanced responsibilities, such as monitoring the progress of people and machines, creating work plans, understanding work progress and load status in real-time, predicting completion times, and optimizing resource allocation in a constantly changing situation. Our WES supports your automation and labor-saving process through cooperation and synergies with your robots and material handling equipment.
Here are three typical use cases.
By visualizing the workload of people and machines from various perspectives you can stay on top of the situation, and reduce costs, by detecting problems and deploying preemptive measures ahead of time.
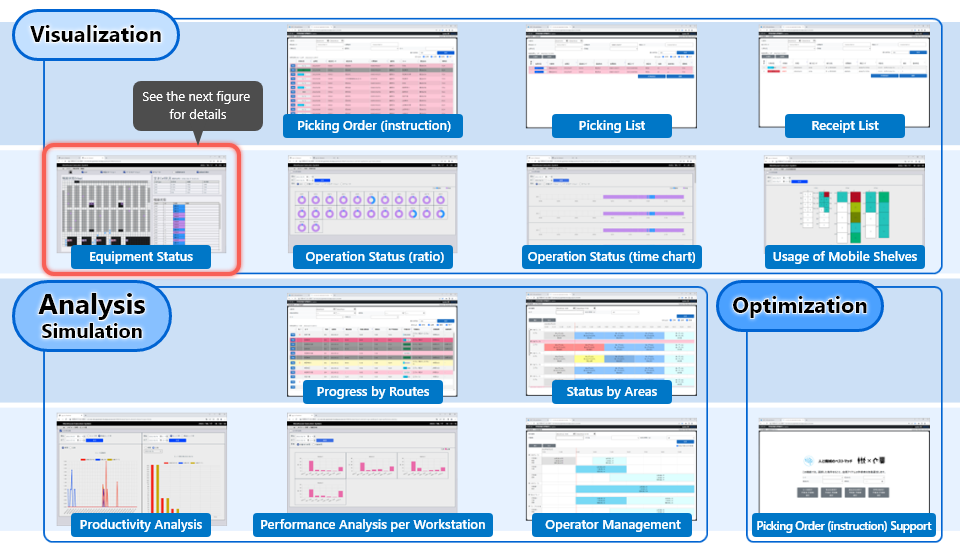
For example, the equipment status screen gives users to have an overview of the shelf transport robots, AGVs, and any failures.
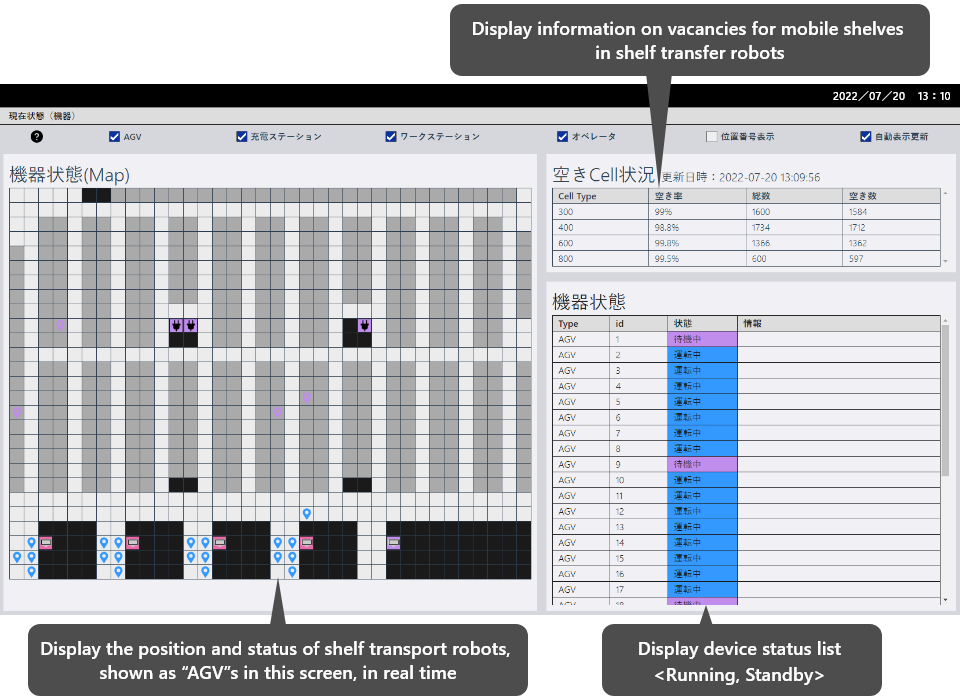
WES predicts work completion times by groups and routes, allowing it to recognize any existing delays, and provides managers with guidance on how to coordinate the workforce when a delay occurs. Early discovery of delays and improved coordination between managers and team members enables efficient work execution and minimizes delays in scheduled vehicle departure times.
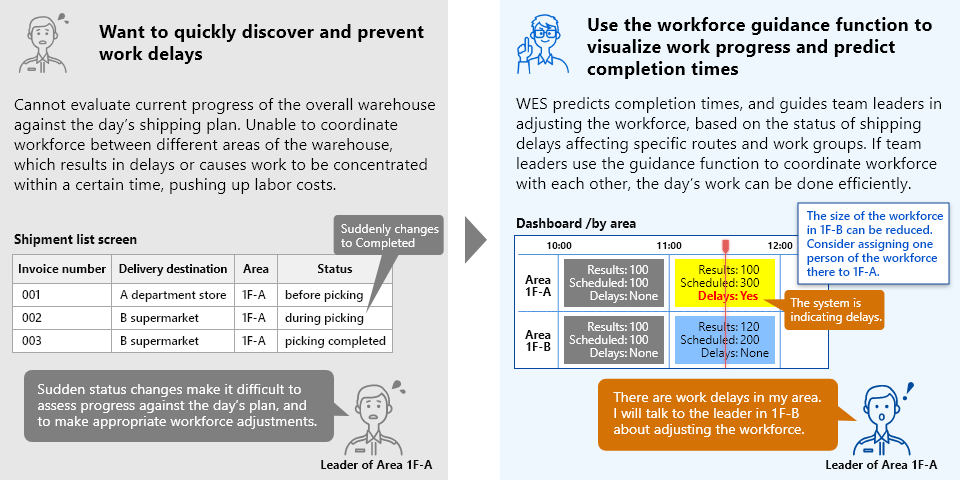
The introduction of automation to warehouses continues, but it is not all plain sailing. Coordination between multiple machines requires manpower and is complex, which becomes a burden on administrators. Installing WES eases that burden, as the WES monitors work progress and optimizes the work plan and operation of each item of equipment. It delivers smooth coordinated control with no need for complicated management, and improves the throughput of the entire warehouse.
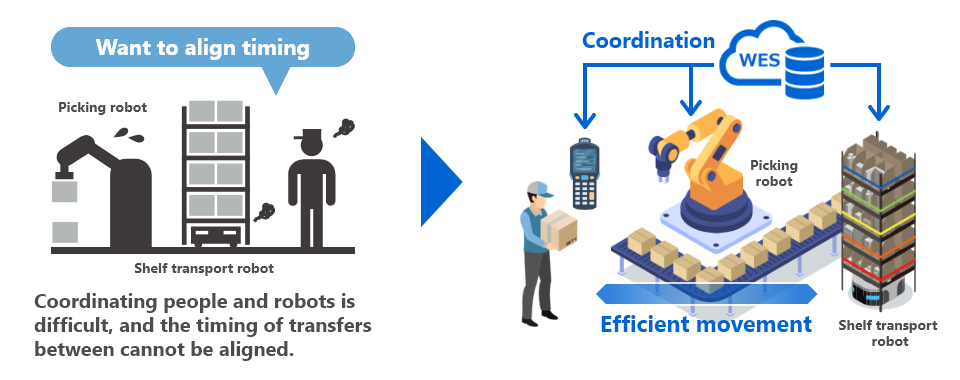
For instance, WES can coordinate people and machines to efficiently complete a single order of multiple products with different shapes. WES does this by evaluating the status of manual picking, picking robots, and shelf transport robots, then assigning the product to manual and automated picking depending on its shape and size.
TOSHIBA SPINEX
The brand name for industrial IoT services compliant with the Toshiba IoT Reference Architecture.
TOSHIBA SPINEX contributes to sustainable value creation. Visit Our strategy.
Thoughts behind the name SPINEX
SPINE + X
The spine is our body’s central support structure, our core, home to the spinal cord that radiates nerves throughout or bodies. In the same way as the nervous system allows us to experience the world, edge computing delivers fast decisions in data processing by distributing sensing and control to every point where it is needed.
Our spine makes us strong and agile. We can do the same for your business, and contribute to society, by providing an essential industrial IoT framework that supports your people and operations with fast, appropriate on-site processing.
The X of SPINEX represents eXperience and eXpansion, and the crossover with other value creators and services. This is how we will create the future with TOSHIBA SPINEX Services.
Two pillars of the Toshiba IoT Reference Architecture compliance standard

